A Step By Step Manufacturing Guide To Plastic Injection Molding Process
Plastic injection molding is an effective system for the manufacture of small and large pieces of plastic with an excellent quality and finish. For this it is essential that the mold has the best qualities, a precise preparation and maximum durability. Among the steps in the manufacture of the molds, the most important is that of the plastic part since it must have a correct and effective design.
The objective of a plastic injection mold is the distribution of molten plastic, to take the correct shape, cooled and then eject the molded part. The distribution channels or castings must be balanced, so that the path of the material is the same for the different cavities, in this way we will obtain a balanced filling of all the cavities and a balanced pressurization of them.
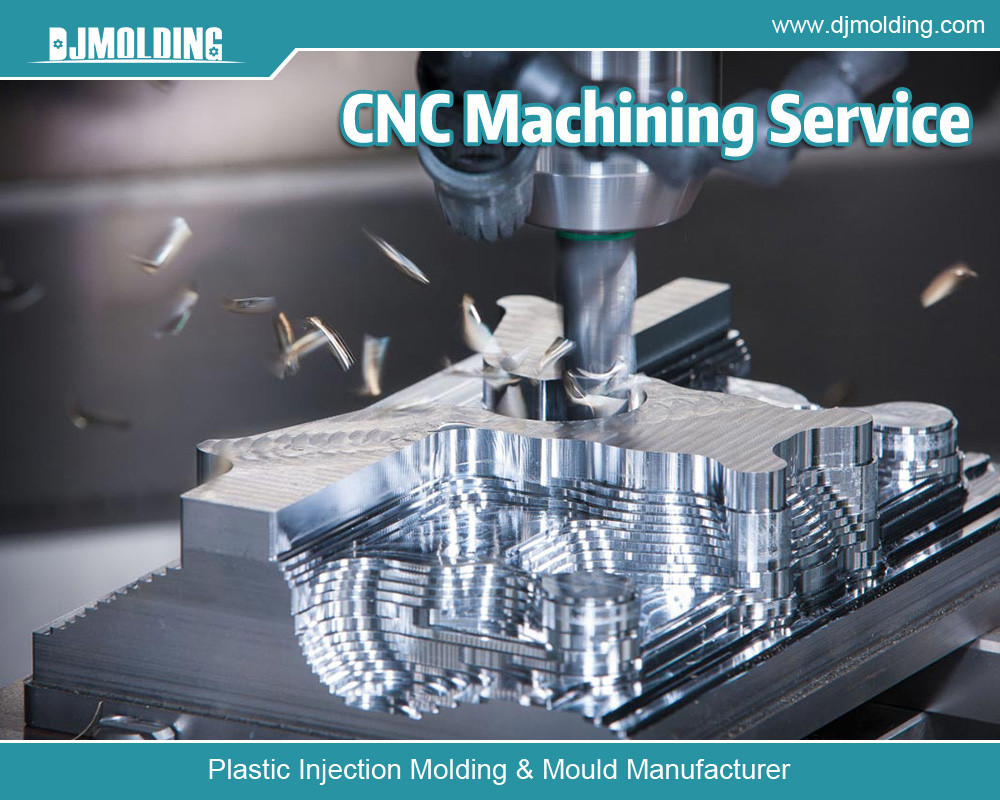
For the correct design of an injection mold it is important to be clear about the following steps:
– Correctly design the plane of the part to be injected, mark the partition lines, injection inlet area, position of the ejectors and any detail of the mold that may facilitate its correct manufacture.
– According to the specifications of the plastic to be used in the mold, it is necessary to take into account shrinkage, flow and abrasion characteristics, molecular structure, thermal behavior, viscosity …
To manufacture a precision injection mold and part, the main points to take into account are the dimensional accuracy with the required tolerances, the material to be used in the molding process and the final finish of the part.
Plastics with low shrinkage present no problem when calculating their final dimension and the dimensions of the mold can be easily calculated to give the final accuracy of the product dimension. Plastics with high shrinkage must be taken with more consideration and study more critical points since it is more complicated when calculating their reaction.
For the manufacture of molds for the injection of plastics, the use of special steels is mandatory, due to the loads they are subjected to.
There is a wide variety of materials for the manufacture of molds for plastic injection Some of the steels used in injection molds are:
- A2: Steel hardened to 58-60 Rockwell C, resists abrasion-
- D2: Steel with more chromium content, more abrasion resistant and more difficult to machine than A2, more brittle, better for small parts.
- D7: Steel with very good resistance to abrasion but more difficult to machine than A2 and D2.
- Stavax and Orvar: Highly recommended for mirror polished molds due to its chrome content and low porosity.
- Motherboards: 1730
- Mold plates: 2311, 2738, P 20.
The costs for the manufacture of the molds are usually high, since the time spent in machining and adjusting them is usually considerable. Furthermore, dimensional accuracy and surface quality are often extremely laborious to achieve.
The final finish of the figure to be injected on many occasions is a very important aspect when deciding on the mold finish. This factor is important for the correct behavior of the plastic and represents an additional cost, being one of the highest final costs in the construction of the molds.
The different finishes that are usually used in injection molds are:
Machining finish: It is divided into two phases, roughing that eliminates the great part of steel and finishing machining that eliminates the remaining material with small passes generating the final finishing surfaces.
EDM: In this case, an electrode is manufactured, usually made of copper or graphite, which removes material from the mold cavity. The electrodes generate electric shocks that remove the steel from the mold leaving the final surface with a different VDI number.
Refined or polished: For this finish, various tools are used that make the surface of the figure of the mold refined with very fine stripes or polished as if it were a mirror.
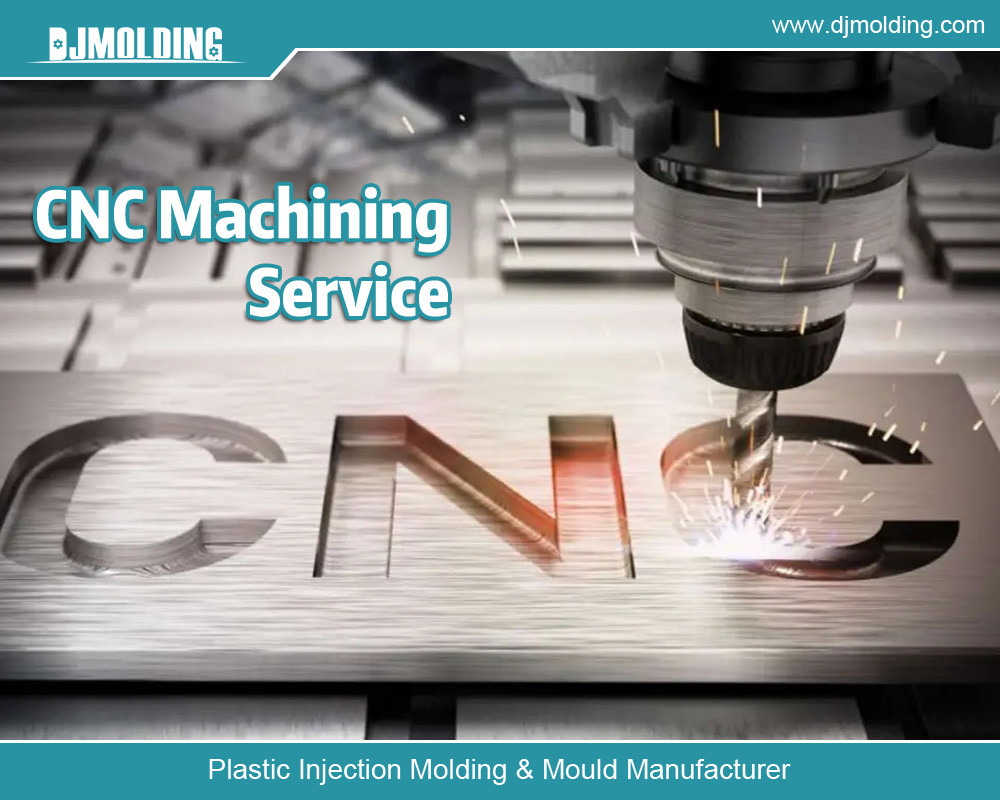
For more about a step by step manufacturing guide to plastic injection molding process,you can pay a visit to Djmolding at https://www.djmolding.com/fundamentals-of-the-plastic-molding-injection-process-for-plastic-part-manufacturing/ for more info.
The post A Step By Step Manufacturing Guide To Plastic Injection Molding Process appeared first on Plastic Injection Molding Manufacturer.